Test site fix up
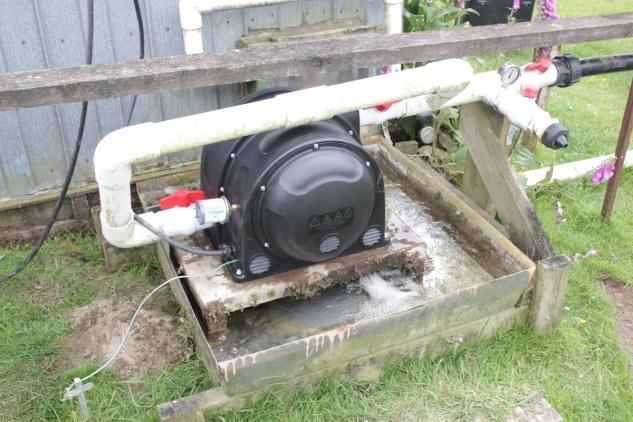
The first PowerSpout PLT ever made (in 2010) went to our 150m test site. Prior to this turbine, our earlier (2005) green-case PLT had also been tested on this site. We abandoned the site in 2013 and gifted the PLT and GTI to the farmer as a thank you for putting up with us over the years.
We got a call recently (I suspect his power bill had gone up) that there was an issue. We decided to send a new PLT to the site so that the old one could be inspected for wear and tear at our factory.
The PLT had run on various GTI’s: SMA Sunnyboy, Windyboy and more recently the Enasolar inverter.
The PLT turbine was very productive, generating 20,855 kWh (DC output) between 19/2/10 and 2/3/2013.
No record of production was kept between 2/3/2013 and January 2014 when the turbine was handed over to the farmer with a new Enasolar GTI. Very little attention was paid to it thereafter until it failed in October 2017 (or a few weeks before). During this 3.5 years it clocked up a further 11,865kWh according to the inverter's internal logging software.
The new PLT200HP turbine when recently installed did 1.7kW. It is run on 1 jet in dry periods so averages 1000-1200W most of the time. Being a test site (also used to test GTI tracking stability) it has been off some of the time and rarely had any service checks as the site is too remote to visit often.
There have been about 32,000 kWh generated that has been logged, and more not logged. The farmer will have saved well in excess of $10,000NZ in the time we have been using this site and should (with a little maintenance) continue to save up to $2600NZ each year.
We inspected the PowerSpout Pelton rotor. Our rotors are injection molded from glass-filled nylon. Many other manufacturers use metal. The question has often been asked “how durable are these plastic rotors compared to other materials”. This site has a high silt burden so has been a good test for the injection molded turbine rotor buckets.
The photo below shows the old rotor alongside a new one. After seven years of arduous operation at the limit of the turbine's operational envelope, the wear on the Pelton runner was only 2mm of material lost from the central ridges. The difference in weight was not measurable (under 5g).
Here for comparison is a photo of a brass Pelton turbine runner after ten years operation on a much lower 30m head site where it produced roughly half the power output of the Totara Valley site. The full story of this one is in a Home Power Magazine article here.
So if you have a client who has read too many internet opinions on this subject of plastic runners you can send them this newsletter.